Een belangrijke innovatie aan het systeem is dat de midcoat en niet de eindcoat uit 3K bestaat.
Kwaliteit is speerpunt
In de strijd tegen beschadigingen gaat Kegro Deuren in Groesbeek zijn deuren na de eerste coating afwerken met een tweede laag 3K-midcoat gevolgd door een 1K-voorlak- of -aflaksysteem. De oppervlaktelaag wordt zo gladder, maar vooral harder. De aangepaste lakstraat is na de bouwvak operationeel.
Terwijl het vakantievierend personeel aan de kust de hitte trotseerde, werkte directeur Jan Kersten van Kegro Deuren in Groesbeek net als vorig jaar in de zomerperiode op zijn kantoor aan de uitwerking van een businessplan voor het komend jaar. “We kijken met zijn allen hoe het beter kan. Tot op het kleinste detailniveau”, aldus Kersten. De inspanningen van het vorig jaar zijn succesvol gebleken. De onderneming schrijft weer zwarte cijfers en realiseerde een groei van 30 procent in het eerste halfjaar 2018 ten opzichte van 2017. Maar Kersten zou Kersten niet zijn als de doelstellingen voor 2019 als gevolg daarvan nog weer een stuk omhoog zijn geschroefd. “Er is circa € 2,5 miljoen gereserveerd voor (al deels) gerealiseerde investeringen in uitvoeringen 2018. Eind 2019 wordt de productie van vlakke deurrompen van Raalte naar een nieuwe fabriek in Groesbeek overgebracht. Hiervoor zal nieuwbouw op het huidige bedrijfsterrein worden gerealiseerd.” Het investeringsbudget 2019 tot Q1 2020 bedraagt € 4 tot 5 miljoen. Kersten: “Er zal ook verdere robotisering plaatsvinden. Kernwoord bij de huidige en toekomstige plannen voor zowel de Kegro-organisatie als het te produceren product is ‘kwaliteit’.”
Massief en vlak
Op het gebied van massieve deuren werkt de onderneming vanwege de stabiliteit uitsluitend met de houtsoorten merbau en sipo mahonie (FSC® en EUTR). Ook het frame van de samengestelde vlakke deuren bestaat volledig uit hardhout (meranti of mahonie) in een breedte van 100 mm. “Hier ondersteunt een inwendige stijl voor additionele stabilisatie, ook in extreme zonlichtbelasting, zonder afbreuk te doen aan de thermische isolatie. We hebben geen problemen meer van uitbuigende deuren.” De samengestelde vlakke deuren vormen een geheel met dekplaat en randhout door deze volledig en zonder luchtinsluitingen met polyurethaan (85-90 kg/m3) te injecteren. Kersten: “De deur is zo 100 procent capillairdicht zodat interne condensatie is uitgesloten.” De deuren zijn voor vorm- en afmetingsstabilisatie verder voorzien van aluminium schilden en Tricoya-dekplaten. De glaslatframes blijven duurzaam dicht door de uitvoering met dubbelezwaluwstaartlijmverbinding. “Op de kunststofpluggen die we sinds vorig jaar in dit systeem toepassen, blijft kracht staan zodat de verstekverbinding altijd dicht blijft. Het is een detail, maar wel een belangrijk detail.”
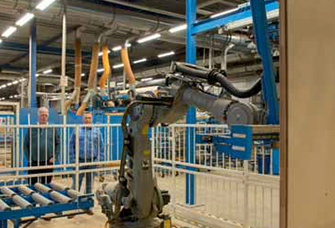
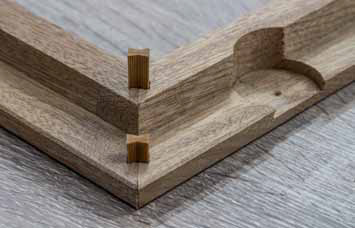
Groot aandachtspunt in het tweede halfjaar 2018 is de reductie van faalkosten. De tweedegeneratiewisseldeur (GEN 2) bewijst inmiddels zijn waarde daarin. Een verfsysteem met een hogere kwaliteitsreserve voor de definitieve deur is daarbij een van de nieuwe uitgangspunten. “We zijn inmiddels een jaar aan het stoeien met een duurzaam verfsysteem”, aldus Kersten. “We hangen 60 tot 70 procent van onze deuren af. De woning is dan lang niet altijd al opgeleverd. Dat betekent bij de bestaande verfsystemen dat de deur bij aanstoten of iets dergelijks gevoelig blijft voor beschadigingen. Ook komt transportschade voor, of aftekeningsschade bij opstapeling van deuren. We hebben twee schilders in dienst om dergelijke problemen het hoofd te bieden.” Om de deuren minder gevoelig voor dergelijke schades te maken, is er sinds september vorig jaar in samenwerking met AkzoNobel gekeken naar een ander verfsysteem. Dat is gelukt. Kersten: “De eerste laag is een standaardflowcoat om de poriën te behandelen. Direct na de bouwvak gaan we beginnen met een tweede laag midcoat uit drie componenten. Deze 3K bestaat uit twee soorten PU-verf en een isocyanaat verharder die in de spuitkop bij elkaar komen. De installaties worden daarvoor omgebouwd.” Het nieuwe systeem betekent ook een nieuwe werkwijze. Kersten: “De deur moet tussen de twee en zes uur 1K-voorlak- of -aflaksysteem opgespoten krijgen. Binnen dat tijdsbestek werkt het isocyanaat nog enigszins hardend op de aflaklaag. De volgende dag kun je in principe dertig deuren op elkaar stapelen zonder te hoeven vrezen voor beschadigingen. De laag is goed gesloten met een waterdampdoorlatendheid tussen de 30 en 40 gram per m2 (de eis is 250 gram per m2 voor voorlak en 150 gram voor aflak, de meeste 1K-systemen zitten op 150 gram/m2, red). Aan het begin van de dagproductie om 6.00 uur wordt de midcoat opgebracht, zodat de voor- of aflaklaag nog dezelfde dag kan volgen. Om een optimale stabiliteit te garanderen, willen we geen vochtverplaatsing in de deur hebben. De elasticiteit van dit systeem blijft voldoende en de harde en gladde afwerking zorgt ervoor dat er minder vuilaanhechting kan plaatsvinden. Bovendien hoeft de deur zo in principe pas in het elfde jaar overgeschilderd te worden. Ik schat zelf in dat we het voorkomen van beschadigen van de laklaag zo met 60 procent zullen reduceren”, aldus Kersten.
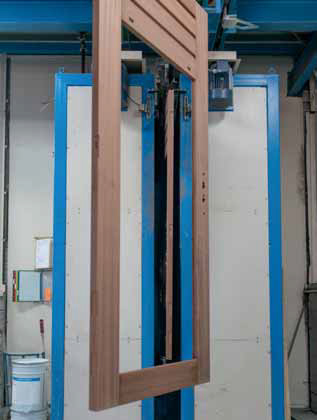
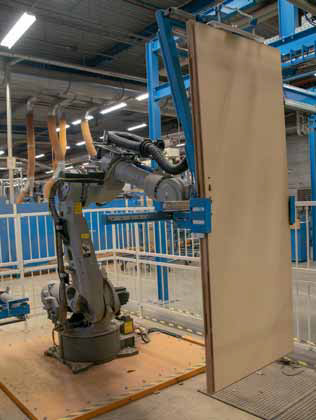
Een belangrijke innovatie aan het systeem is dat de midcoat, en niet de eindcoat uit 3K bestaat. Kersten: “2K wordt in andere branches veelvuldig toegepast als eindlaag, maar bij deuren betekent dit het gevaar van een slechte hechting bij overschilderen. Door de voor- of aflak binnen twee tot zes uur daarna te doen, heb je dat probleem niet en reageert het isocyanaat nog op de toplaag. Additioneel opschuren kan achterwege blijven, al doen we het nog wel.” In de huidige lakinstallatie worden twee tussenstations gemonteerd. Het spuiten zelf zal elektrostatisch zijn, met airmix en niet langer airless. “Hoe lager de druk is, hoe beter de verf om de ronde kanten van de deur trekt”, aldus Kersten. “We realiseren zo een optimale kantendekking.” Ook zal er een optimalisatie in de droogtunnel gedaan worden, waardoor de lak sneller en gelijkmatiger van binnenuit doordroogd en sneller handelbaar is voor het verdere proces.
Krimp en zwel
Met deze kwaliteitsslag verwacht Kersten ook een oplossing te hebben gevonden voor het probleem van beschadigingen en krimp/uitzetten van de deuren in complete gevelelementen in de nieuwbouw. “Die worden vaak ingepakt in plastic naar de bouw vervoerd en maken daarna alsnog een lange bouwfase mee. De folie die is bedoeld voor de mechanische beschadiging heeft echter een onbedoeld microklimaateffect. Door hitteopbouw op zonnige dagen ontstaat luchtcirculatie zodat het element als het ware in een droogtunnelsituatie belandt. Wij hebben deze zomer deuren gemeten waar als gevolg daarvan de houtvochtigheid was gedaald tot 7 procent. In herfst en winter loop je met de dichte folie een grotere kans op condensatie. Deze afwerklaag sluit de deur afdoende op, al kan een open folie bij elk ander verfsysteem ook al veel krimp- en zwelleed voorkomen. Al werkt een folie altijd negatief voor microklimaat. Lange belasting met folie zal altijd leiden tot meer werking.”
Bron: Vakblad Timmerfabrikant, editie 9 2018